Чтобы доставить такой агрегат заказчику, требуется довольно сложная транспортная операция. Огромный реактор весом в десятки тонн с ювелирной точностью грузят в трейлер, и дальше ему предстоит путь на предприятие, где его смонтируют, подключат, и химико-технологический процесс, что называется, пойдёт. На днях АО «ЗАВКОМ», традиционно известное в Тамбове как завод «Комсомолец», отгрузило несколько таких реакторов для АО «Воронежсинтезкаучук», где они станут основным оборудованием технологической цепочки грандиозного проекта ТЭП-100, который станет по-своему революционным для отечественной химической промышленности. И сердцем проекта являются агрегаты, сделанные на тамбовском предприятии, чья марка хорошо известна по всей России и во всём мире. А причина такой уникальной востребованности — самый современный технологический уровень продукции и её высочайшее качество, которое коллектив «Комсомольца» традиционно гарантирует.
Человеку непосвящённому это трудно представить, но внутренняя поверхность этого огромного реактора представляет собой идеально отполированный металл с точностью до долей микрона. Таковы технологические требования к установке, где будут идти сложные химические процессы. Причём внутри проходят многочисленные змеевики и патрубки, изготовление и монтаж которых в свою очередь требует ювелирной точности и качества, от чего зависит не просто работа оборудования, но и безопасность. Это не первые агрегаты, поставленные мастерами АО «ЗАВКОМ» для проекта ТЭП-100, где установка техники ведётся под контролем шеф-инженера из Германии, и о качестве продукции из Тамбова у требовательных заказчиков отзывы без преувеличения самые восторженные. Хотя добиться такого уровня совсем непросто, и на «Комсомольце» для этого создана своя по-своему уникальная система контроля качества всего, что производится на предприятии.
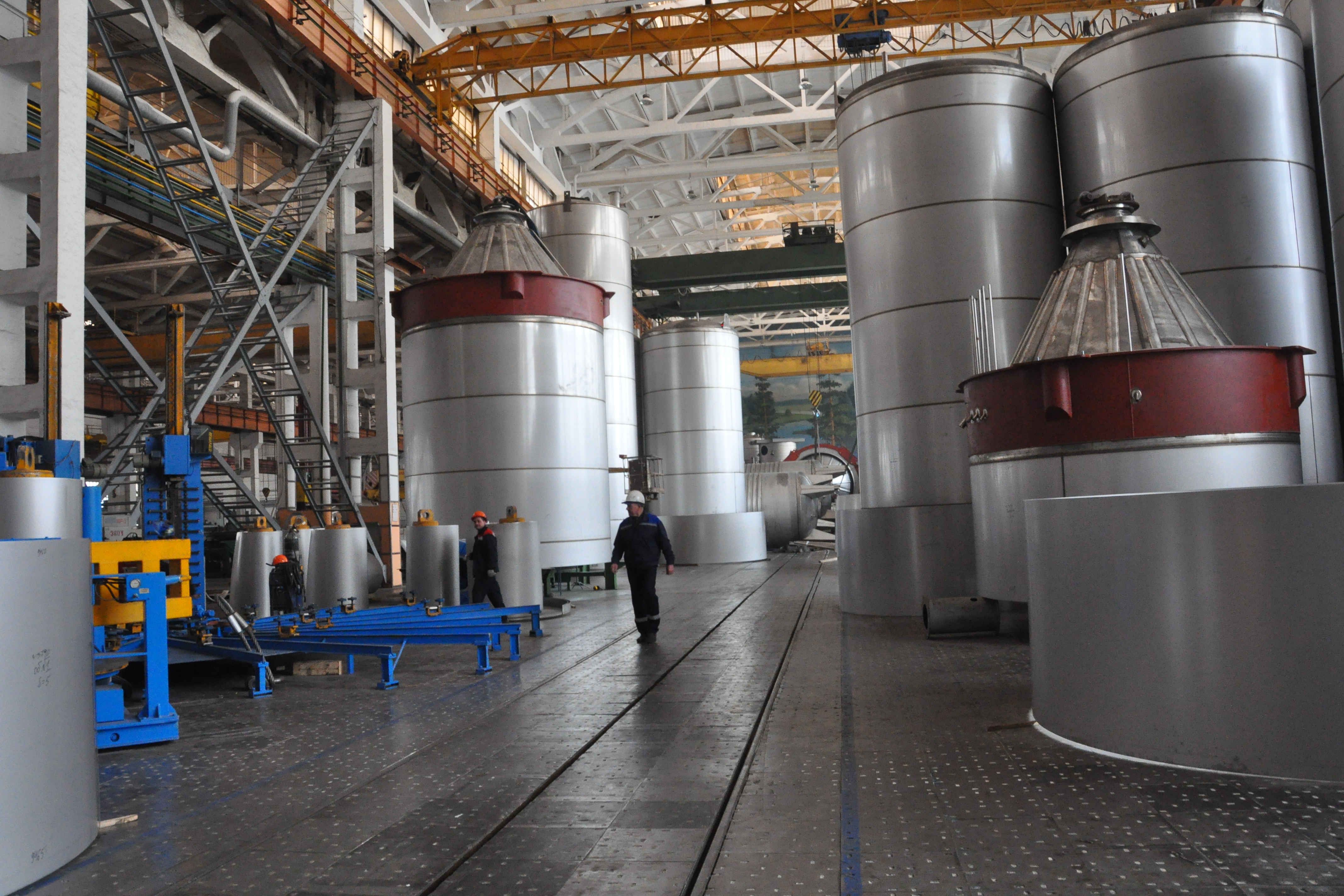
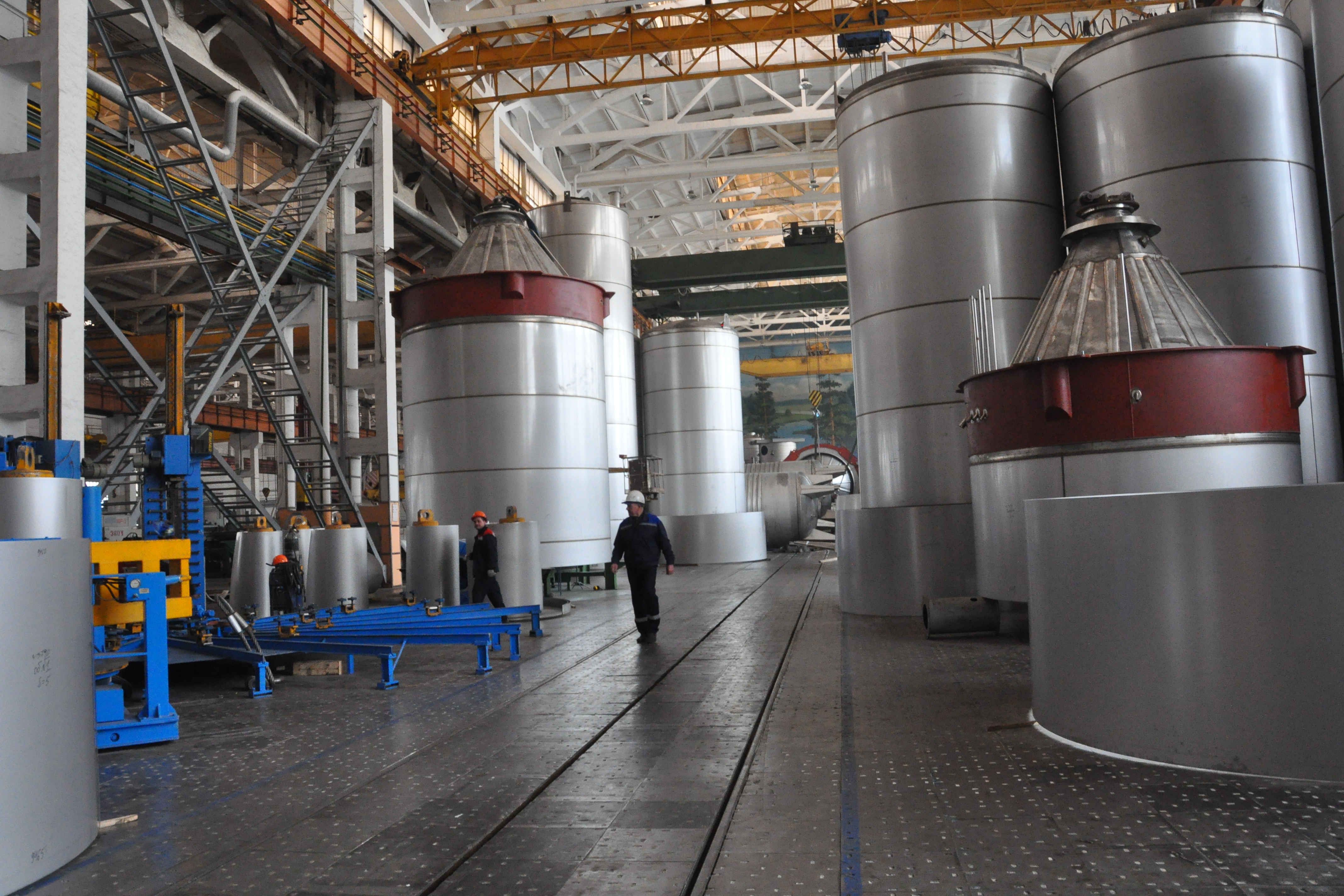
Качество продукции как мировой авторитет
Несмотря на относительно скромную площадь, занимаемую заводом, где территория жёстко ограничена городскими кварталами, изделия его весьма внушительны по размерам и обеспечивают химическую, нефтехимическую, пищевую и даже атомную отрасли России и других стран. А среди них как наши партнёры из ближнего зарубежья, так и из самого дальнего, включая заказчиков в виде известных фирм и концернов Европы и Азии, где особо бурными темпами развивающаяся химическая промышленность Индии и Китая оказалась весьма заинтересованной именно в тамбовском оборудовании. Это не говоря уже об атомных электростанциях, например, таких, как Шанхайская в Китае или АЭС в иранском Бушере, агрегаты для которых создаются на тамбовском заводе «Комсомолец». Причём это агрегаты, нейтрализующие в случае аварии процесс на станции и обеспечивающие аварийное охлаждение реактора, отчего напрямую зависят безопасность и жизнь людей. А доброе имя и деловой авторитет предприятия нарабатываются годами, и чтобы держать планку на уровне, надо самим быть на уровне. В этом уверен директор по качеству Василий Сисев, ну а для гордости за это самое качество у него есть все основания.
«Качество продукции у нас начинается с маркетинга. То есть требования заказчика должны сочетаться с нашими возможностями. Требования эти сейчас очень высокие, и если мы хотим оставаться успешными на рынке и на равных конкурировать с лучшими мировыми производителями, то должны своё оборудование и свою систему контроля качества постоянно совершенствовать. Этот стимул не позволяет успокаиваться, и это, строго говоря, и обеспечивает прогресс и технический, и экономический. А заказы у нас самые разные, каждый раз что-то новое. И для их выполнения даже приходится приобретать специальное оборудование, как, например, в процессе изготовления агрегатов для Центра имени Курчатова. Это и ответственно, но это и очень интересно. Такая вот творческая работа», — считает Василий Алексеевич.
Впрочем, это творчество регулируется весьма строгими стандартами качества, на которые предприятие имеет специальные сертификаты. Это в первую очередь международный стандарт ISO-900, а также аттестация соответствия требованиям ASME, полученная в 2015 году в США. При этом стоит учитывать, что это вовсе не документ, выданный раз и навсегда, — эти высокие мировые требования надо постоянно подтверждать. В прошедшем году предприятие прошло переаттестацию на стандарты ASME, что расширило возможности производства не только на его непосредственной территории, но и при монтаже оборудования на площадках заказчиков. АО «ЗАВКОМ» получило право на фирменное клеймо ASME — своего рода международный «знак качества», говорящий об авторитете предприятия и, конечно, обеспечивающий спрос на его продукцию в мире. Пока завод «Комсомолец» является единственным тамбовским промышленным предприятием, имеющим такой знак, да и по всей России счёт его обладателей идёт на единицы.
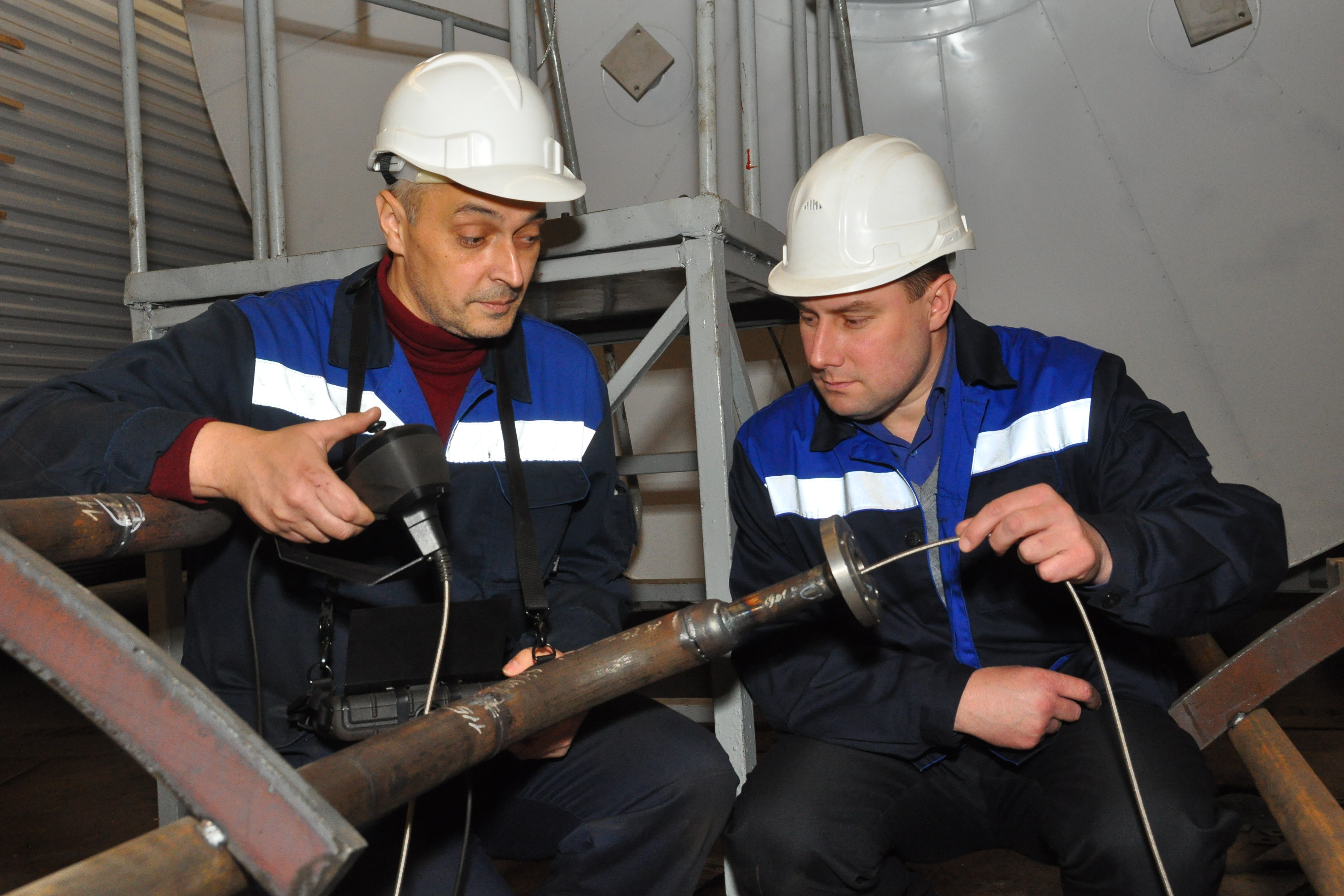
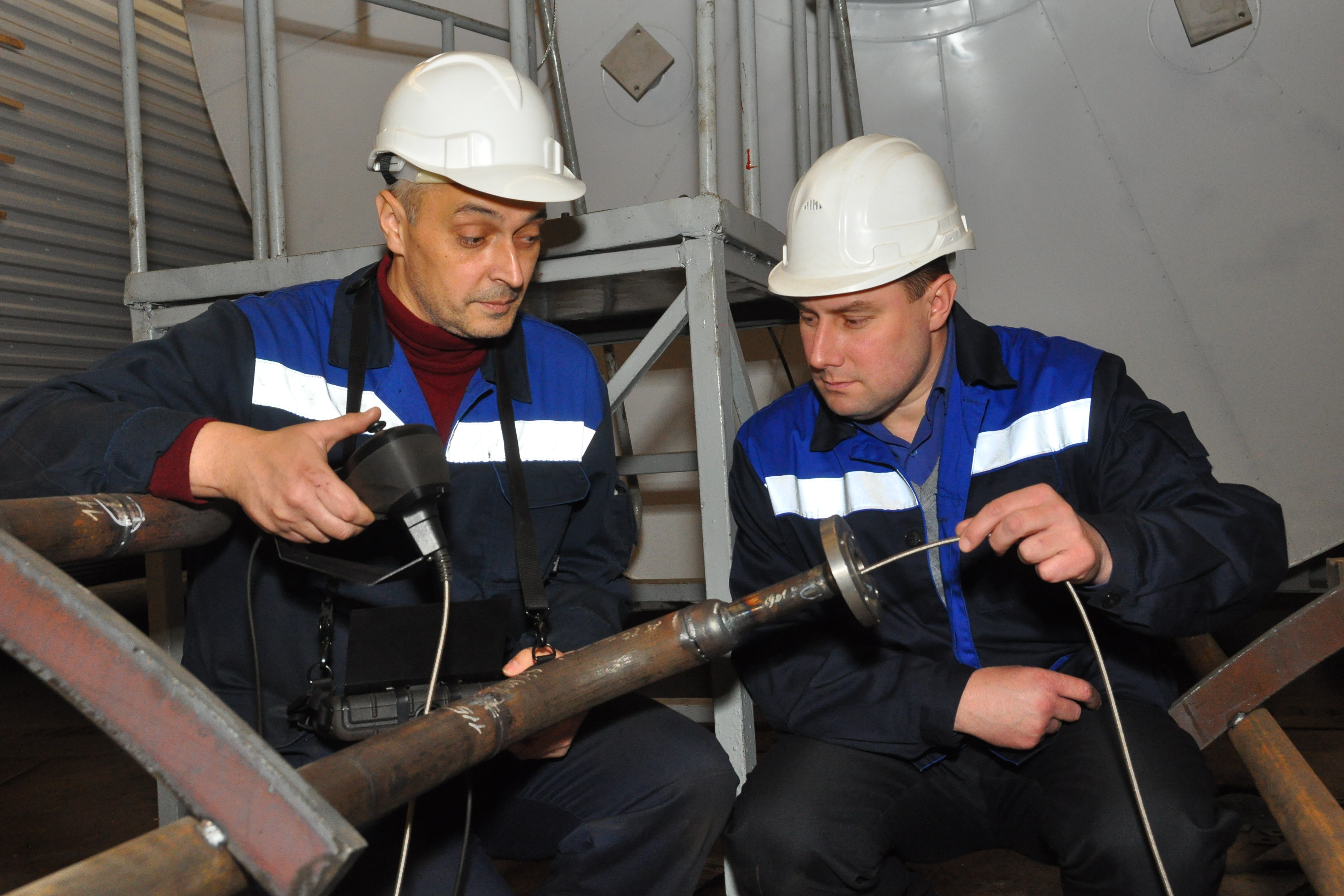
УЗК для металла
Понятно, чтобы обеспечивать столь высокие стандарты, на заводе создана не просто целая система, следящая за качеством продукции, но и применяется специальное и во многом абсолютно уникальное оборудование. Собственно, оно и позволяет обеспечивать трёхступенчатую систему контроля от рабочего до мастера и затем уже до специалистов самого отдела технического контроля. Более шестидесяти процентов объёма всех работ на заводе — это сварка. Самая разная, включая автоматическую, позволяющая сваривать различные виды стали, биметаллов, меди, причём листы разной толщины — от одного до ста миллиметров. Кстати, здесь, на этом поприще, трудятся и женщины, чья аккуратность и скрупулёзность при этих операциях оказываются просто незаменимы. И это не случайно, ведь аппаратам, что делают на «Комсомольце», приходится работать в агрессивных средах при высокой температуре. И здесь контроль качества — это уже во многом вопрос безопасности.
Ну а чтобы определить качество сварных швов, чистоты обработки поверхности, герметичность и прочие необходимые параметры, на предприятии применяются самые современные приборы. Например, для того чтобы определить, насколько соответствуют стандартам внутренние части многочисленных змеевиков и патрубков сложных агрегатов, используются специальные эндоскопы с портативными видеокамерами, позволяющими видеть на мониторе все тонкости этих изделий, требующих весьма тонкой работы.
А вот для контроля качества полировки поверхностей не менее хитрый прибор под названием профилометр, который с точностью до микрона позволяет выявить все неровности, которых в данном случае просто не должно быть.
В Центральной заводской лаборатории металл, из которого делаются выпускаемые реакторы и другие аппараты, в самом прямом смысле просвечивают насквозь. В принципе это напоминает процедуру обследования пациента в кабинете врача. Образец металла проходит рентген, правда, по интенсивности излучения не сравнимый с рентгеном, применяемым в медицинских целях. Так что находиться во время «просвечивания» в помещении, где установлен прибор, людям категорически запрещено. И, наконец, для определения качества металла в лаборатории используется всем знакомое УЗК.
Конечно, помощнее и совершеннее, чем в кабинете врача, но диагноз металлу этот способ даёт очень точный. И это особо важно — качество металла является условием заказчика, а чтобы его выполнить, эти материалы часто приходится закупать за рубежом и, естественно, подвергать тщательному контролю как на входе, так и на выходе уже в виде готовых изделий. Это не говоря уже об определении химического состава материалов с помощью рентгенофлюорисцентного химанализатора и других поистине фантастических приборов, с которыми здесь на ты специалисты, а это люди заинтересованные, увлечённые, в основном люди молодые и по-настоящему креативные.
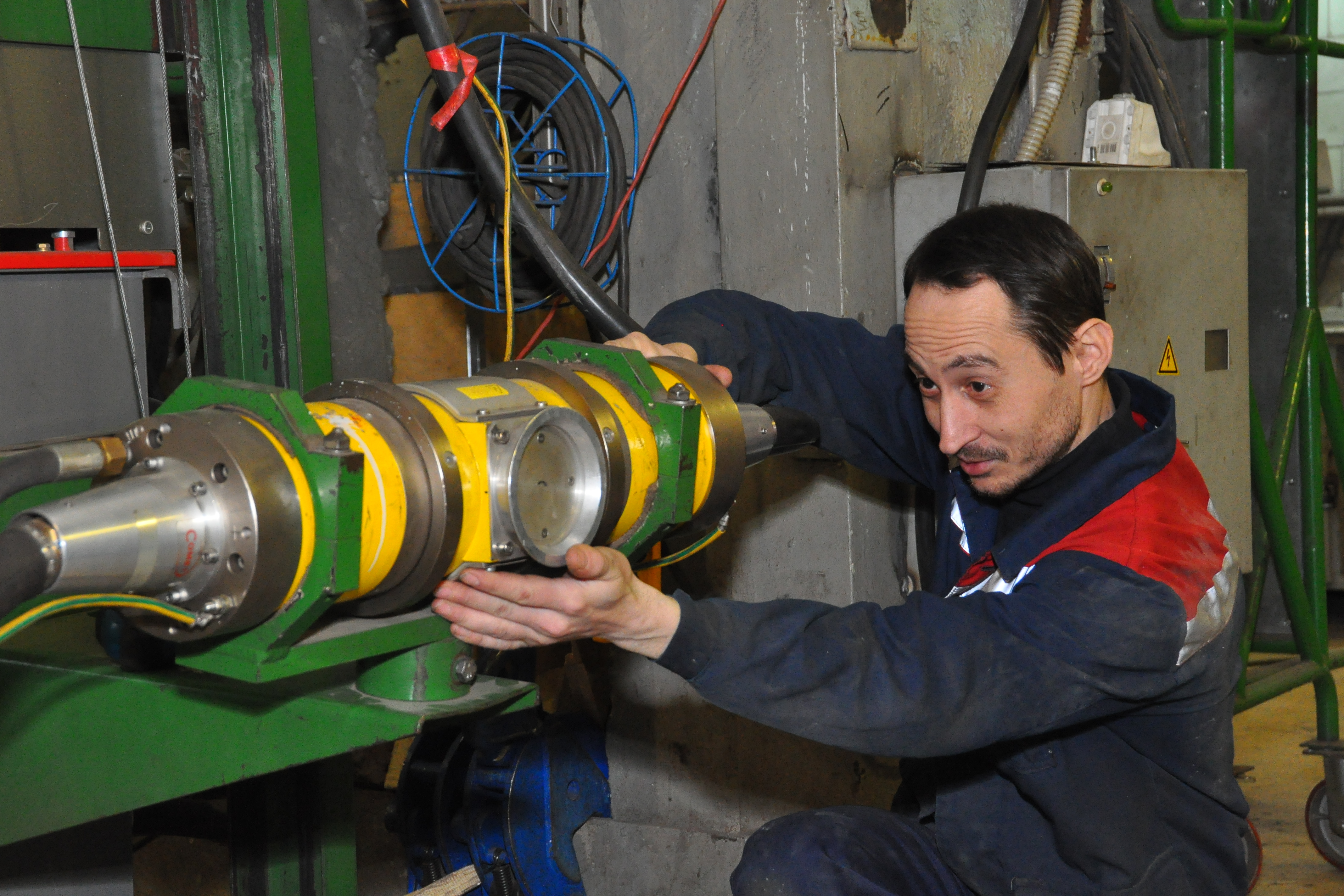
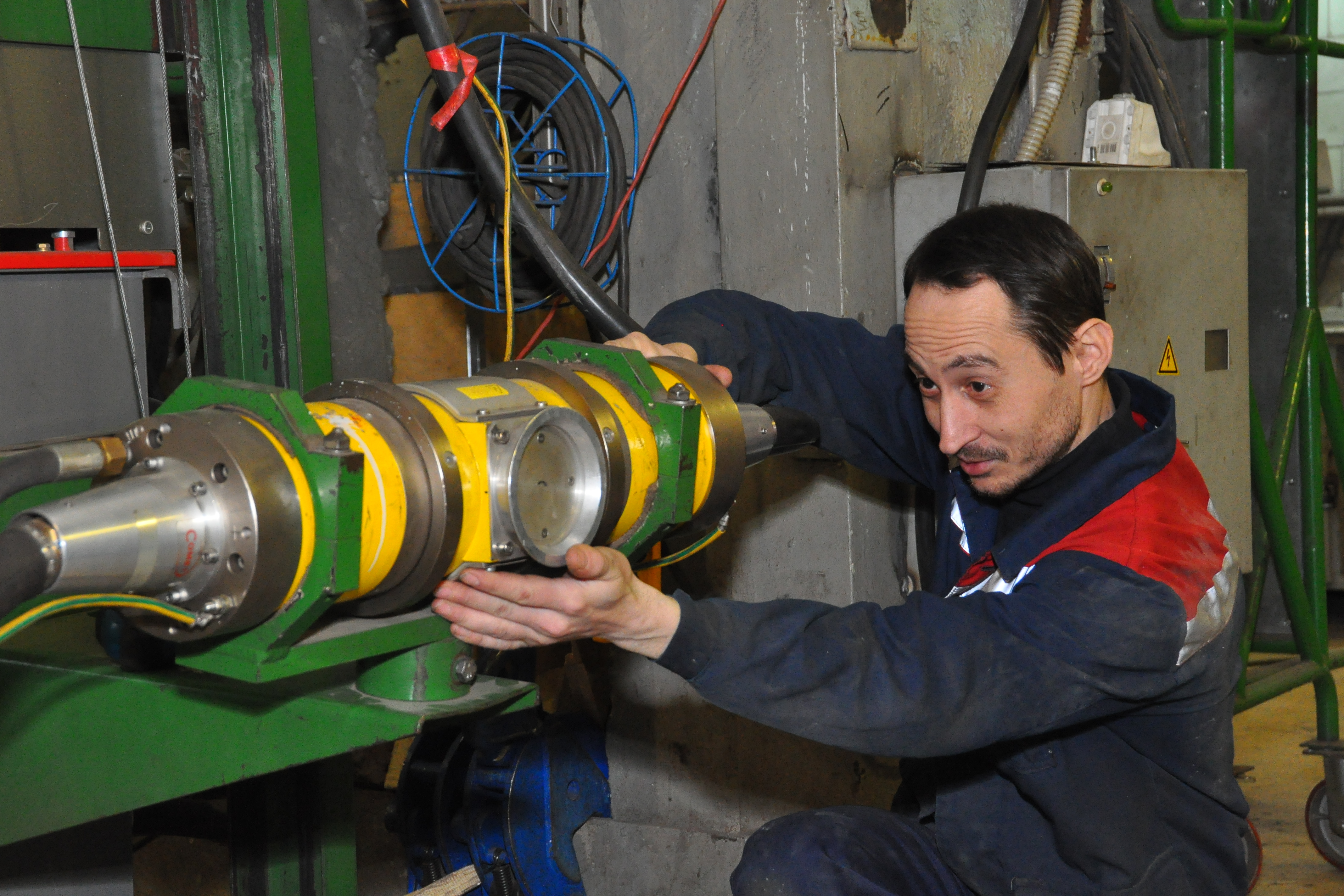
Кадры решают всё
Случайных людей здесь действительно не бывает. Просто потому, что при столь сложной и скрупулёзной работе, которой является контроль качества продукции завода, их просто быть не может. Кто-то приходит после окончания вуза, обычно ТГТУ, с которым у предприятия давно налажены тесные связи. Студенты здесь проходят производственную практику, и самые лучшие, а главное, заинтересованные, остаются. Как Александр Прохоров, пришедший на завод девятнадцать лет назад в качестве инженера-конструктора, а теперь возглавляющий бюро технического контроля заготовительного, механического цехов, также входного контроля. И, как признался Александр, работу эту не променяет ни на что, потому что интересная она. Каждый раз новые заказы и новые аппараты, не похожие на предыдущие, так что не соскучишься. Да и одним родным Тамбовом сфера деятельности не ограничивается — для контроля качества монтажа приходится выезжать к заказчикам в разные города, так что повезло увидеть почти всю страну.
А вот Олег Юдин пришёл на «Комсомолец» в непростом 1994 году простым слесарем-кабельщиком второго разряда. Немногие молодые люди тогда шли в рабочие, особенно на производство, в перспективы которого многие не верили. А он поверил, увидев здесь особый креативный настрой. И не просто поверил, а постоянно повышал квалификацию, осваивал новые специальности и, окончив ТГТУ, стал начальником сборочного цеха, а сейчас является ведущим контрольным мастером ОТК, специалистом, что называется, на вес золота.
Впрочем, таких специалистов здесь немало. Как считает руководитель заводской контрольной лаборатории Вадим Айдаров, залог этого как раз в первую очередь заинтересованность и любовь к делу: «Без этого ничего не выйдет, я сразу предупреждаю, когда приходит новичок, — работа непростая, и расслабиться на ней невозможно. Но если человек влился в это дело, то оно у него пойдёт. И тогда получается коллектив, ответственный и творческий».
Наверное, этот коллектив, сложившийся на этом уникальном тамбовском предприятии, и является главным гарантом не просто качества его продукции, но и будущего завода, успешно прошедшего проверку самым трудным временем. Хотя, наверное, не зря говорят, что своё будущее за нас не создаст никто.